Player FM uygulamasıyla çevrimdışı Player FM !
R&D Test Systems Builds Massive 25 MW Main Bearing Test Facility
Manage episode 448914004 series 2912702
In this episode, Peter Winther, Key Account Manager at R&D Test Systems, discusses the construction of the world’s most powerful main bearing test facility at the Lindø Offshore Renewable Center in Denmark. Winther provides fascinating insights into the engineering challenges and scale of this groundbreaking 25-megawatt facility, including details about its massive concrete foundation and the specialized testing capabilities designed to simulate decades of wear in just months.
Sign up now for Uptime Tech News, our weekly email update on all things wind technology. This episode is sponsored by Weather Guard Lightning Tech. Learn more about Weather Guard’s StrikeTape Wind Turbine LPS retrofit. Follow the show on Facebook, YouTube, Twitter, Linkedin and visit Weather Guard on the web. And subscribe to Rosemary Barnes’ YouTube channel here. Have a question we can answer on the show? Email us!
Pardalote Consulting – https://www.pardaloteconsulting.com
Weather Guard Lightning Tech – www.weatherguardwind.com
Intelstor – https://www.intelstor.com
Wind Energy O&M Australia Conference – https://www.windaustralia.com
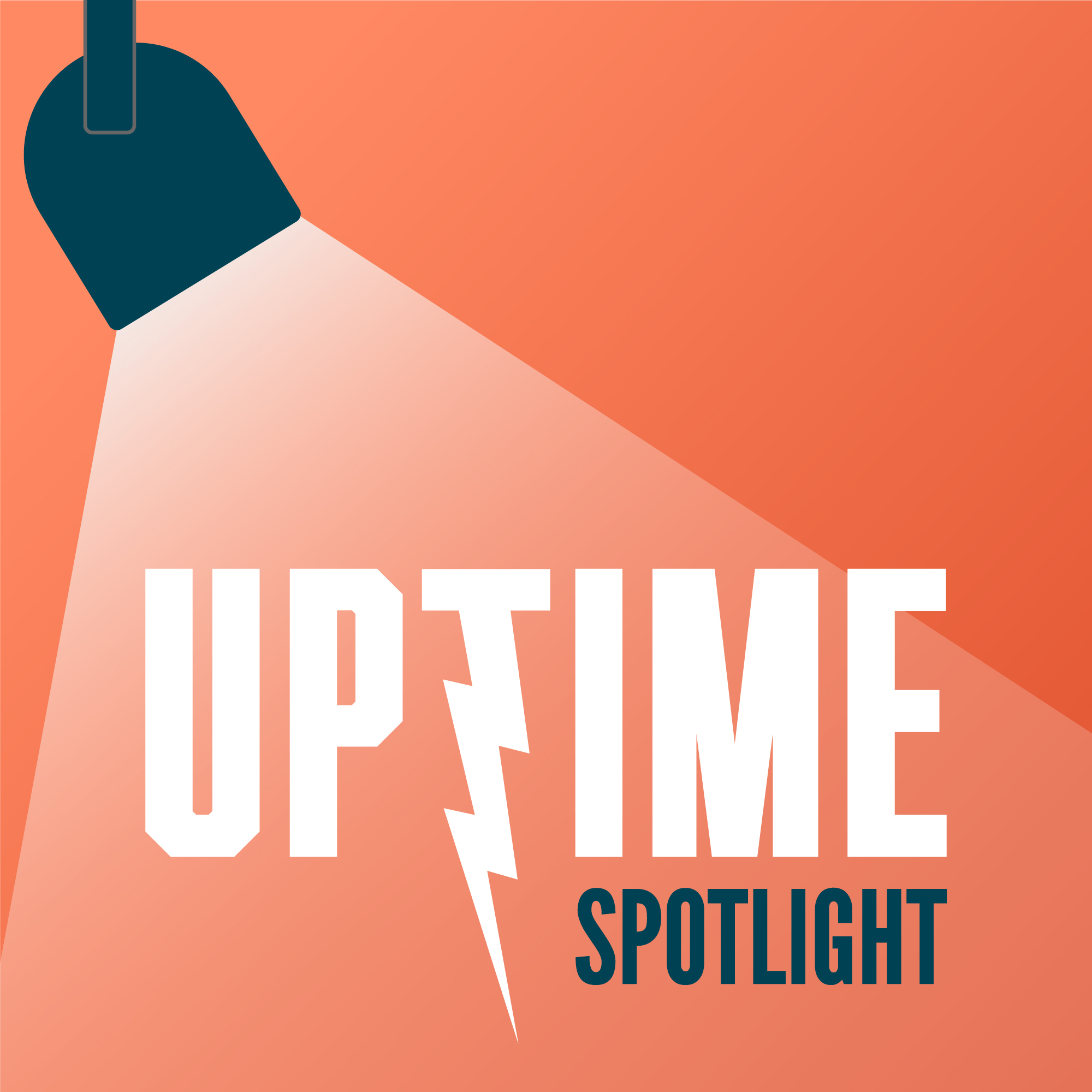
Welcome to Uptime Spotlight, shining light on wind energy’s brightest innovators. This is the Progress Powering Tomorrow.
Allen Hall: Today we’re joined by Peter Winther, Key Account Manager at R& D Test Systems, a company that’s revolutionizing how we test wind turbine components. R& D Test Systems is currently building the world’s most powerful main bearing test facility at the Lindo Offshore Renewable Center in Denmark. They have already delivered the largest halt test bench for nacelle testing at the same location and now these facilities are pushing the boundaries of what’s possible in wind turbine testing with capabilities up to 25 megawatts.
Peter brings extensive experience in large scale test system development and has been instrumental in multiple groundbreaking projects at LORC. Peter, welcome to the show. Thank you very much. Thank you for having me. All right, so you’re building a 25 megawatt main bearing test system. Facility. That’s big.
That’s very big. So just give it a sense of scale. How big is a 25 megawatt bearing?
Peter Winther: The bearing itself, I would guess the inside diameter is more than four meters in a typical bearing constellation. The test bench on the other high, on the other side is also relatively big to be able to break that bearing or bearings, depending on what you’re testing.
The test bench itself pretty big. First of all, features a pretty decent size concrete block or foundation at the bottom, which is roundabout 35 meters long. It took 30 hours to cast the whole thing. It was a one continuous process. We had 280 trucks coming in and they were coming in every six minutes.
And so we basically took all, I think, concrete production from Fyn, which is the island where Ålensø or the test bench is being realized. And then we had back off plants in case the plant went down because if you start casting, you can’t stop, you need to go ahead. You can’t have a cold joint.
Yeah. Yeah. So that’s the foundation itself. An essential thing when you make a foundation like this is also to make sure it cools in the right manner. You can’t just cast it and then go away and then come back in an hour or a week and then all is fine because then you risk not having.
The right material properties throughout the foundation. So we had a more than one megawatt cooling system, making sure that the cross-sectional temperatures throughout different cross sec cross-sections and the foundation was right and not too much of a difference, so we didn’t get cracks and creeping and unwanted properties at the end because you, you can’t really get rid of it.
Allen Hall: When you take this project on, how many engineering challenges are there? Obviously building the. Concrete Foundation by itself is a massive undertaking. How many, how do you break this down and how many big hurdles are there? We’re
Peter Winther: in the lucky position that it’s not, you can say, the first time we’re building a big test rig.
It’s the first time we’re building one that should break a 25 megawatt wind turbine main bearing arrangement. So that’s a first. We have some conceptual building blocks, which we of course relied upon, but it’s, the biggest we’ve ever made. So there’s always challenges. And it’s especially challenging when we need to break something very fast that is at the limit of what is possible to manufacture at this point in time.
There’s a reason why they’re challenged with making 15 or 25 megawatt turbines or whatever they’re saying they can manufacture now. It’s because the, you need also the technology to make bearings sufficiently big enough machining. that you can machine the whole thing. And we need To break something that is intended for 20, 25 years of operation, we need to try to break that in 6 to 12 months.
So it’s a bit of an engineering undertaking to figure out, okay, how do we make our test bench capable of doing that 24 7, also for 20 years.
Allen Hall: I’m curious because you’ve already built a 25 megawatt HALT, Highly Accelerated Lifecycle Testing. At the LORC. And that’s there. So what was the need for a separate facility for the main bearing?
What about main bearings makes the requirements a little bit different?
Peter Winther: You can say in some areas the the 25 megawatt halt, It’s used for validation testing, so that is actually for testing the entire drivetrain, meaning the DUT is an abbreviation we use, device under testing in this case it’s the nacelle.
And for the 25 megawatt HALT test bench, we have already commissioned and there’s an operation over there. It’s also Test the gearbox and the generator which mean we need to be able to apply a pretty significant amount of torque. Also, you wanna stress test the gearbox. Ergo you want to have a lot of torque for the main bearing for the main bearing test bench.
That is not the case. You only have to overcome the friction in the bearings because they don’t see the torque. The torque goes through the main shaft to the gearbox at the back end, in case of a geared solution, and if not, then it’s directly to the generator, but that’s where, why the bearings are there.
So it is actually, It’s overdoing it to test main bearings on the 25 megawatt Holt, because then you pay for a huge direct drive motor in this case, which you don’t need
Allen Hall: in the test. That makes total sense. Okay. And the issues that the industry is having with main bearings is pretty evident and onshore right now there’s a lot of issues in the United States at the moment.
But when we get offshore, that becomes even more critical as 25 megawatt turbines going to repair that gets increasingly difficult. So this is a really key piece of equipment. For offshore wind, isn’t this probably the linchpin to success out on the ocean? It’s at
Peter Winther: least very difficult to change if something goes wrong.
Let’s put it like, everything is difficult to change offshore, but the main bearing arrangement, everything is attached to that in some way, more or less. It’s the connection between the rotating part and the tower. To some extent, so you need to take off a lot of stuff if you are to change the main bearing arrangement or the main bearings.
So yeah, there’s a lot of challenges there and I guess what is evident and what they see is, it is extremely important to test the bearings under the right conditions. What they actually experience in one, in the real life, to get as close to that as possible, which is also what has been the focus.
Focus on this test benches is the main bearing units. We don’t test main bearing standalone, just a bearing, and then turn it around and try to bend it because it is very important, the housing around it, how the load is distributed in the bearings. What is it exposed to in the real life? You need to get as close to that as possible.
So that has also been one of the things. Focuses for this main bearing test bench is it’s main bearing unit. It’s main bearing systems We need to test.
Joel Saxum: Is it actually easier for the main bearing to support the load while it’s spinning? Or when it’s static, the actual hub.
Peter Winther: It is when it’s spinning. And I guess that’s because you, if you have the large load, when it’s static, you risk that the oil is not properly distributed in the bearings and so on.
So ideally, if you have the big loads, I’m pretty sure that the bearings would prefer to rotate. So in
Joel Saxum: this case, okay, now we’re talking testing them. How do you. Okay, so when we talk to this a little bit off air, you explain to us like the test rig and what the hydraulic rams look like to put pressure on it in different ways.
Do you do rotating testing and static testing with this thing for an accelerated lifetime test, or how does that work?
Peter Winther: At the end of the day, it’s of course up to the customer. They’re the experts in how to test their bearings. But on the other hand, we are also trying not to limit them and what they can test.
So it is also something we’ve been discussing with them, what their needs are in this area also. But. Ultimately, we also use bearings so we have the same challenges and the same limitations. All, some of our bearings, at least for the turbines that’s going on right now, our bearings are still somewhat bigger.
We cannot at least we also put in some constraints and say, okay, if you want to do static testing, then it might not be full load or it might not be full load for several days or whatever, as again, we need to make sure that The large equipment doesn’t break but again, we also need to enable the customer to, to take their tests or their designs to the limit.
Joel Saxum: But that’s, that’s an R& D specialty, right? That’s what you guys do. You link up with whoever needs the test benches, whoever needs the testing mechanisms, and you say Okay, let’s get yours, your specific design criteria and what you guys want to do. And we’re going to engineer this thing bespoke to you, but that throws in a bunch of other challenges for you guys as well, because now we’re talking about testing four meter diameter main bearings, but you have a rotating rig yourself.
So you have to have a bearing that’s bigger and stronger than that.
Peter Winther: Yes, that is always a challenge. And as you said Joel we start, it’s also above my head here, the winning concept. So it’s not like we come with a given product or a given solution that fits all testing needs.
We usually start together with a customer, with a blank piece of paper and then figure out, okay, you have a given test needs or an idea at least. And then we figure out it along the way and then we find the winning concept. When we start with. different concepts. Of course, we have a track record and we have proofs, different concepts that use different concepts.
And there are some of them we’ve used several times because they’re suitable for scaling up. And then We mature that along with the customer and make it sure it’s capable of fulfilling the customer’s requirements. But it is a challenge that we need to break the largest bearings that are being manufactured while still using
Allen Hall: bearings in our rake.
Where do you draw the line at Peter? They come in and say, I need a 25 megawatt bearing test center. And you say,
Peter Winther: it’s the, at the end of the day, it’s the customer wallet, the customer’s wallet that draws the line.
Allen Hall: Good reason.
Peter Winther: We could make it bigger if needed, but again it’s also how big are they going to get and how much do we need to future prove?
And so we usually don’t draw a line. We always try to find solutions. The same with the 25 megawatt Holtz test bench we talked about previously. At that point in time, we couldn’t get a solution. Get our hands on a direct drive motor of that size. So we had to design and engineer and manufacture it ourself because that was the need for the given test bench.
So we don’t say okay, you want to go above 25. Keep us out of it. It is usually also a financial decision. We also had bigger on the table but bigger is more expensive. So it’s always also refers back to yeah, the investment on the business case and
Allen Hall: how much of a 25 megawatt main bearing test rig.
is designed by R& D test systems that is unique to that test bench. 95,
Peter Winther: 99 percent of the control system is based on common industry you could say control, hardware, software stuff, the foundation, one of a kind the main shaft, we, one of a kind the bearings actually also. Order of one of a kind.
The housing is of course also one of a kind. The hydraulic cylinders, they’re made to spec. So it’s not something we’re taking from a serial production. It’s made to us and it’s made to what we need for this one. As some of the biggest hydraulic actuators in the bench, they can, each of them apply more than 1000 ton.
Wow.
Allen Hall: That requires a team of engineers. What does that staff look like? The project team
Peter Winther: peak was We are in manufacturing phase. We are having things manufactured and also soon delivered outside. So we are actually On the other side of the peak where all the engineering was carried out. But I guess 30, 40 engineers working on them.
That seems like not enough. It is actually.
Allen Hall: Yeah. So because you’ve done it before you have it honed. And so there, there are multiple phases to this. And as a project person, how does that work? Like the customer picks up the phone, calls you and says, I need a 25 megawatt main bearing test facility. And someone takes that phone call.
How does it, what happens from there?
Peter Winther: Usually they’re not that specific, but they send out a request at least. We have some testing needs. If we can start with let’s say we start with a feasibility study and figure out together with the customer what do we, what do they need? And What sort of concept is the winning concept and so on.
So if they call, depending on which number they call and so on, but they would probably start with me as I’m a sales representative, a key account manager, so I would be in that process as well. And then taking it all the way to telling the customer what the thing actually costs. You can say part of that journey is also there is always at the beginning, everything is need to have.
That’s it. But when you put a price tag on what the different requirements cost, some of them become nice to have. That’s also some of the journey we have with them together. For this one, for example there was one particular load case which had some pretty aggressive dynamics. And Dynamics, when we have hydraulics, we need a pretty big HPU, so that one load case implied the HPU had to be tripled compared to all the other load cases.
So all of a sudden, that given requirement became a nice to have because they could just bend three times as long, that was okay with them so lowering the frequency. And then. At some point, then we get to the point where, okay, they have the requirements, we have the solution and we’re satisfied, they’re satisfied with the solution.
In this case, it was a joint three party venture. Because we are the test bench realizer. Our customer is Log, which is a commercial test center. And their customer on the other side, that’s Sheffler. From Germany. So it was you can say a bit odd because it was, the requirements were actually coming from Schaeffler through Locke, but to us, but we were all working together on it to find, okay, now this design fulfills the requirements and this is then the cost of it, how we go ahead and we were, and then.
Internally in R& D, we hand it over to operations. That’s what we call it which realizes it. So they take it from purchase order and then all the way to hand over to the customer.
Allen Hall: So there’s two questions there. How long did it take to iron out the specifications with everybody at the table? How many months was that?
And then once you decide to build it. How long does it take to actually, to complete a project?
Peter Winther: So from, you can say we start to, it’s going to be completed. Building is around about 24 months. The process leading up to that. So the sales process was, also, I would say delayed. It was quite long and it was influenced by some probably some geopolitical situation going on in some part of Europe where, yeah, something happened at some point which changed priorities at the customer.
So it took Actually years I would say. Because one thing is settling on the requirements. Another thing is also it’s a big investment. So committing to that, that, that takes some time. Is it quicker to build than it is to specify then? Not at all. I don’t, when, once we got, there was a big pause.
So that’s, that shouldn’t be part of that. So once we got into the specification phase, it was a, it was a pretty intense months. But really good cooperation between the three of us.
Allen Hall: And RD is going to open the facility. in 2025. 2025. Yes. So how soon before it then becomes commissioned and ready to take that first main bearing, is it ready to go day one there?
Peter Winther: That’s the intention. Yes. The expectation. So right now, process wise we’ve left site, we’ve made the foundation and now we’ve stepped back a little bit. And now the building is being erected around it. It’s easier to make the big concrete block first and then build the building around it.
So they’re making the floor as we speak, they might finish that already. And then they’ll build the walls around it and then come start next year. It’s the intention. We’ll come back in and start installing auxiliaries and the test load unit and.
Joel Saxum: You know you’re making a big piece of kit when the building has to be built around it.
Allen Hall: So obviously R& D Test Systems is the leader in big test equipment and building these test benches. There’s, you do impressive work. How much is on your plate at the minute? You have this 25 megawatt facility going in. Are there other things already in the pipeline to, that you haven’t even announced yet?
That, that. You’re working on. How busy are you right
Peter Winther: now? We’re busy realizing the projects we have. And, unfortunately, I’m not allowed to tell too much about the pipeline, but we definitely have some interesting stuff going on. That’s for sure.
Allen Hall: That’s the beauty of R& D test systems. If you need somebody to build a piece of test equipment for big machines, you And do it right.
I would imagine there’s only one place to go and that’s R& D test systems. And you’re going to have to get ahold of Peter because Peter is their salesperson.
Peter Winther: Give me a call. I’m not the only one, but I can promise our sales organization, our sales team will take good care of you. If you have that particular need, we’ll love to help you solve it.
How do they reach you? How do they contact you? We have our webpage on rdas. dk where there’s a contact information where they can reach us.
Allen Hall: Yeah. And Peter’s available on LinkedIn. So if you get desperate and you need to have a 25 megawatt main bearing test facility built in your backyard or 30,
you just reach out to Peter, he’s ready to take your phone call. And I, every time R& D test systems comes on the podcast, I’m always impressed because You’re doing such amazing things and it’s such a benefit to the industry and congratulations on that. Come on. I know how hard that is to do and I know how successful these test benches have been.
That’s truly amazing. So Peter, thank you for being on the podcast. It’s been wonderful to have you.
Peter Winther: We’re just a small piece of the puzzle and we’re just helping, trying to help this green transition and yeah, having wind succeed because it’s awesome.
378 bölüm
Manage episode 448914004 series 2912702
In this episode, Peter Winther, Key Account Manager at R&D Test Systems, discusses the construction of the world’s most powerful main bearing test facility at the Lindø Offshore Renewable Center in Denmark. Winther provides fascinating insights into the engineering challenges and scale of this groundbreaking 25-megawatt facility, including details about its massive concrete foundation and the specialized testing capabilities designed to simulate decades of wear in just months.
Sign up now for Uptime Tech News, our weekly email update on all things wind technology. This episode is sponsored by Weather Guard Lightning Tech. Learn more about Weather Guard’s StrikeTape Wind Turbine LPS retrofit. Follow the show on Facebook, YouTube, Twitter, Linkedin and visit Weather Guard on the web. And subscribe to Rosemary Barnes’ YouTube channel here. Have a question we can answer on the show? Email us!
Pardalote Consulting – https://www.pardaloteconsulting.com
Weather Guard Lightning Tech – www.weatherguardwind.com
Intelstor – https://www.intelstor.com
Wind Energy O&M Australia Conference – https://www.windaustralia.com
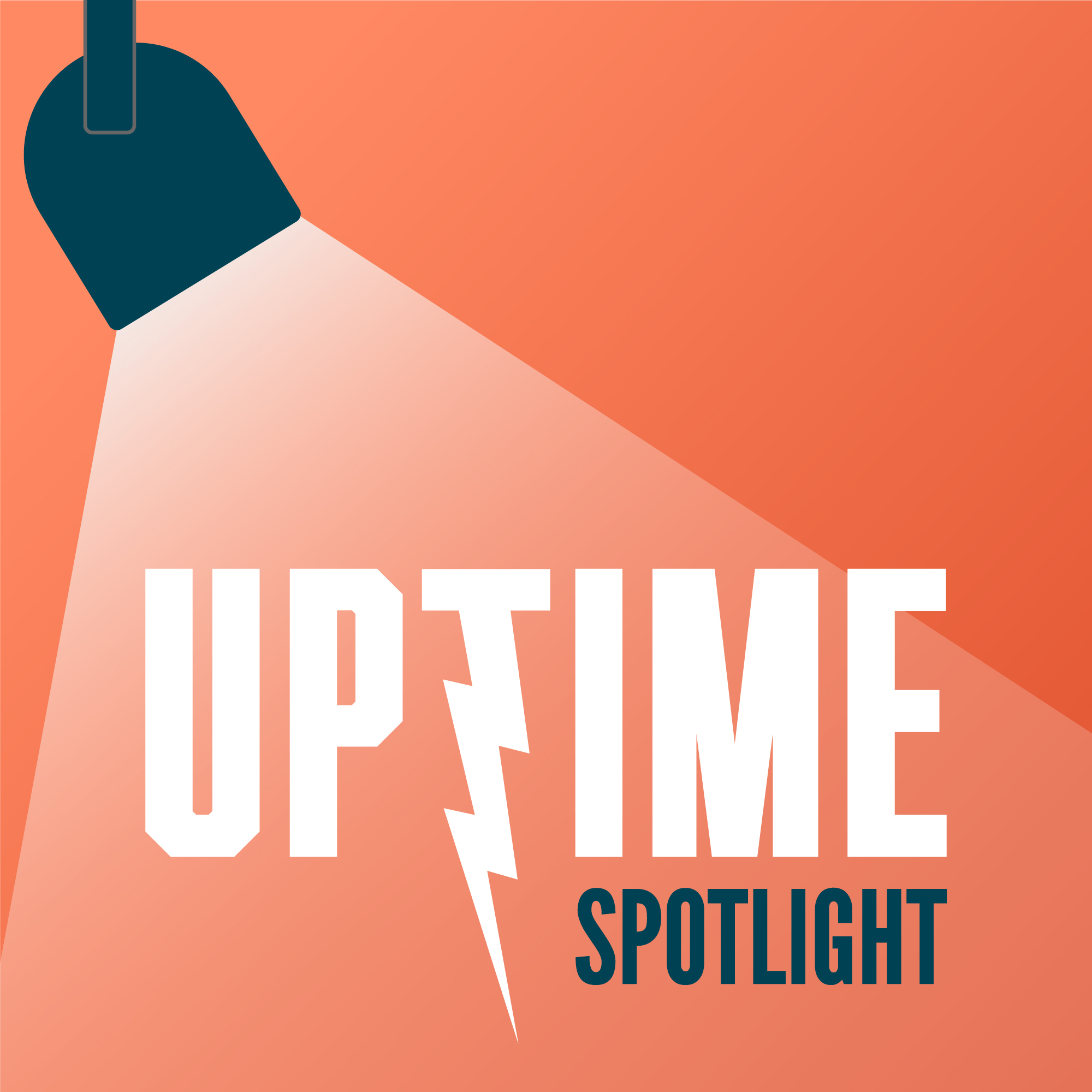
Welcome to Uptime Spotlight, shining light on wind energy’s brightest innovators. This is the Progress Powering Tomorrow.
Allen Hall: Today we’re joined by Peter Winther, Key Account Manager at R& D Test Systems, a company that’s revolutionizing how we test wind turbine components. R& D Test Systems is currently building the world’s most powerful main bearing test facility at the Lindo Offshore Renewable Center in Denmark. They have already delivered the largest halt test bench for nacelle testing at the same location and now these facilities are pushing the boundaries of what’s possible in wind turbine testing with capabilities up to 25 megawatts.
Peter brings extensive experience in large scale test system development and has been instrumental in multiple groundbreaking projects at LORC. Peter, welcome to the show. Thank you very much. Thank you for having me. All right, so you’re building a 25 megawatt main bearing test system. Facility. That’s big.
That’s very big. So just give it a sense of scale. How big is a 25 megawatt bearing?
Peter Winther: The bearing itself, I would guess the inside diameter is more than four meters in a typical bearing constellation. The test bench on the other high, on the other side is also relatively big to be able to break that bearing or bearings, depending on what you’re testing.
The test bench itself pretty big. First of all, features a pretty decent size concrete block or foundation at the bottom, which is roundabout 35 meters long. It took 30 hours to cast the whole thing. It was a one continuous process. We had 280 trucks coming in and they were coming in every six minutes.
And so we basically took all, I think, concrete production from Fyn, which is the island where Ålensø or the test bench is being realized. And then we had back off plants in case the plant went down because if you start casting, you can’t stop, you need to go ahead. You can’t have a cold joint.
Yeah. Yeah. So that’s the foundation itself. An essential thing when you make a foundation like this is also to make sure it cools in the right manner. You can’t just cast it and then go away and then come back in an hour or a week and then all is fine because then you risk not having.
The right material properties throughout the foundation. So we had a more than one megawatt cooling system, making sure that the cross-sectional temperatures throughout different cross sec cross-sections and the foundation was right and not too much of a difference, so we didn’t get cracks and creeping and unwanted properties at the end because you, you can’t really get rid of it.
Allen Hall: When you take this project on, how many engineering challenges are there? Obviously building the. Concrete Foundation by itself is a massive undertaking. How many, how do you break this down and how many big hurdles are there? We’re
Peter Winther: in the lucky position that it’s not, you can say, the first time we’re building a big test rig.
It’s the first time we’re building one that should break a 25 megawatt wind turbine main bearing arrangement. So that’s a first. We have some conceptual building blocks, which we of course relied upon, but it’s, the biggest we’ve ever made. So there’s always challenges. And it’s especially challenging when we need to break something very fast that is at the limit of what is possible to manufacture at this point in time.
There’s a reason why they’re challenged with making 15 or 25 megawatt turbines or whatever they’re saying they can manufacture now. It’s because the, you need also the technology to make bearings sufficiently big enough machining. that you can machine the whole thing. And we need To break something that is intended for 20, 25 years of operation, we need to try to break that in 6 to 12 months.
So it’s a bit of an engineering undertaking to figure out, okay, how do we make our test bench capable of doing that 24 7, also for 20 years.
Allen Hall: I’m curious because you’ve already built a 25 megawatt HALT, Highly Accelerated Lifecycle Testing. At the LORC. And that’s there. So what was the need for a separate facility for the main bearing?
What about main bearings makes the requirements a little bit different?
Peter Winther: You can say in some areas the the 25 megawatt halt, It’s used for validation testing, so that is actually for testing the entire drivetrain, meaning the DUT is an abbreviation we use, device under testing in this case it’s the nacelle.
And for the 25 megawatt HALT test bench, we have already commissioned and there’s an operation over there. It’s also Test the gearbox and the generator which mean we need to be able to apply a pretty significant amount of torque. Also, you wanna stress test the gearbox. Ergo you want to have a lot of torque for the main bearing for the main bearing test bench.
That is not the case. You only have to overcome the friction in the bearings because they don’t see the torque. The torque goes through the main shaft to the gearbox at the back end, in case of a geared solution, and if not, then it’s directly to the generator, but that’s where, why the bearings are there.
So it is actually, It’s overdoing it to test main bearings on the 25 megawatt Holt, because then you pay for a huge direct drive motor in this case, which you don’t need
Allen Hall: in the test. That makes total sense. Okay. And the issues that the industry is having with main bearings is pretty evident and onshore right now there’s a lot of issues in the United States at the moment.
But when we get offshore, that becomes even more critical as 25 megawatt turbines going to repair that gets increasingly difficult. So this is a really key piece of equipment. For offshore wind, isn’t this probably the linchpin to success out on the ocean? It’s at
Peter Winther: least very difficult to change if something goes wrong.
Let’s put it like, everything is difficult to change offshore, but the main bearing arrangement, everything is attached to that in some way, more or less. It’s the connection between the rotating part and the tower. To some extent, so you need to take off a lot of stuff if you are to change the main bearing arrangement or the main bearings.
So yeah, there’s a lot of challenges there and I guess what is evident and what they see is, it is extremely important to test the bearings under the right conditions. What they actually experience in one, in the real life, to get as close to that as possible, which is also what has been the focus.
Focus on this test benches is the main bearing units. We don’t test main bearing standalone, just a bearing, and then turn it around and try to bend it because it is very important, the housing around it, how the load is distributed in the bearings. What is it exposed to in the real life? You need to get as close to that as possible.
So that has also been one of the things. Focuses for this main bearing test bench is it’s main bearing unit. It’s main bearing systems We need to test.
Joel Saxum: Is it actually easier for the main bearing to support the load while it’s spinning? Or when it’s static, the actual hub.
Peter Winther: It is when it’s spinning. And I guess that’s because you, if you have the large load, when it’s static, you risk that the oil is not properly distributed in the bearings and so on.
So ideally, if you have the big loads, I’m pretty sure that the bearings would prefer to rotate. So in
Joel Saxum: this case, okay, now we’re talking testing them. How do you. Okay, so when we talk to this a little bit off air, you explain to us like the test rig and what the hydraulic rams look like to put pressure on it in different ways.
Do you do rotating testing and static testing with this thing for an accelerated lifetime test, or how does that work?
Peter Winther: At the end of the day, it’s of course up to the customer. They’re the experts in how to test their bearings. But on the other hand, we are also trying not to limit them and what they can test.
So it is also something we’ve been discussing with them, what their needs are in this area also. But. Ultimately, we also use bearings so we have the same challenges and the same limitations. All, some of our bearings, at least for the turbines that’s going on right now, our bearings are still somewhat bigger.
We cannot at least we also put in some constraints and say, okay, if you want to do static testing, then it might not be full load or it might not be full load for several days or whatever, as again, we need to make sure that The large equipment doesn’t break but again, we also need to enable the customer to, to take their tests or their designs to the limit.
Joel Saxum: But that’s, that’s an R& D specialty, right? That’s what you guys do. You link up with whoever needs the test benches, whoever needs the testing mechanisms, and you say Okay, let’s get yours, your specific design criteria and what you guys want to do. And we’re going to engineer this thing bespoke to you, but that throws in a bunch of other challenges for you guys as well, because now we’re talking about testing four meter diameter main bearings, but you have a rotating rig yourself.
So you have to have a bearing that’s bigger and stronger than that.
Peter Winther: Yes, that is always a challenge. And as you said Joel we start, it’s also above my head here, the winning concept. So it’s not like we come with a given product or a given solution that fits all testing needs.
We usually start together with a customer, with a blank piece of paper and then figure out, okay, you have a given test needs or an idea at least. And then we figure out it along the way and then we find the winning concept. When we start with. different concepts. Of course, we have a track record and we have proofs, different concepts that use different concepts.
And there are some of them we’ve used several times because they’re suitable for scaling up. And then We mature that along with the customer and make it sure it’s capable of fulfilling the customer’s requirements. But it is a challenge that we need to break the largest bearings that are being manufactured while still using
Allen Hall: bearings in our rake.
Where do you draw the line at Peter? They come in and say, I need a 25 megawatt bearing test center. And you say,
Peter Winther: it’s the, at the end of the day, it’s the customer wallet, the customer’s wallet that draws the line.
Allen Hall: Good reason.
Peter Winther: We could make it bigger if needed, but again it’s also how big are they going to get and how much do we need to future prove?
And so we usually don’t draw a line. We always try to find solutions. The same with the 25 megawatt Holtz test bench we talked about previously. At that point in time, we couldn’t get a solution. Get our hands on a direct drive motor of that size. So we had to design and engineer and manufacture it ourself because that was the need for the given test bench.
So we don’t say okay, you want to go above 25. Keep us out of it. It is usually also a financial decision. We also had bigger on the table but bigger is more expensive. So it’s always also refers back to yeah, the investment on the business case and
Allen Hall: how much of a 25 megawatt main bearing test rig.
is designed by R& D test systems that is unique to that test bench. 95,
Peter Winther: 99 percent of the control system is based on common industry you could say control, hardware, software stuff, the foundation, one of a kind the main shaft, we, one of a kind the bearings actually also. Order of one of a kind.
The housing is of course also one of a kind. The hydraulic cylinders, they’re made to spec. So it’s not something we’re taking from a serial production. It’s made to us and it’s made to what we need for this one. As some of the biggest hydraulic actuators in the bench, they can, each of them apply more than 1000 ton.
Wow.
Allen Hall: That requires a team of engineers. What does that staff look like? The project team
Peter Winther: peak was We are in manufacturing phase. We are having things manufactured and also soon delivered outside. So we are actually On the other side of the peak where all the engineering was carried out. But I guess 30, 40 engineers working on them.
That seems like not enough. It is actually.
Allen Hall: Yeah. So because you’ve done it before you have it honed. And so there, there are multiple phases to this. And as a project person, how does that work? Like the customer picks up the phone, calls you and says, I need a 25 megawatt main bearing test facility. And someone takes that phone call.
How does it, what happens from there?
Peter Winther: Usually they’re not that specific, but they send out a request at least. We have some testing needs. If we can start with let’s say we start with a feasibility study and figure out together with the customer what do we, what do they need? And What sort of concept is the winning concept and so on.
So if they call, depending on which number they call and so on, but they would probably start with me as I’m a sales representative, a key account manager, so I would be in that process as well. And then taking it all the way to telling the customer what the thing actually costs. You can say part of that journey is also there is always at the beginning, everything is need to have.
That’s it. But when you put a price tag on what the different requirements cost, some of them become nice to have. That’s also some of the journey we have with them together. For this one, for example there was one particular load case which had some pretty aggressive dynamics. And Dynamics, when we have hydraulics, we need a pretty big HPU, so that one load case implied the HPU had to be tripled compared to all the other load cases.
So all of a sudden, that given requirement became a nice to have because they could just bend three times as long, that was okay with them so lowering the frequency. And then. At some point, then we get to the point where, okay, they have the requirements, we have the solution and we’re satisfied, they’re satisfied with the solution.
In this case, it was a joint three party venture. Because we are the test bench realizer. Our customer is Log, which is a commercial test center. And their customer on the other side, that’s Sheffler. From Germany. So it was you can say a bit odd because it was, the requirements were actually coming from Schaeffler through Locke, but to us, but we were all working together on it to find, okay, now this design fulfills the requirements and this is then the cost of it, how we go ahead and we were, and then.
Internally in R& D, we hand it over to operations. That’s what we call it which realizes it. So they take it from purchase order and then all the way to hand over to the customer.
Allen Hall: So there’s two questions there. How long did it take to iron out the specifications with everybody at the table? How many months was that?
And then once you decide to build it. How long does it take to actually, to complete a project?
Peter Winther: So from, you can say we start to, it’s going to be completed. Building is around about 24 months. The process leading up to that. So the sales process was, also, I would say delayed. It was quite long and it was influenced by some probably some geopolitical situation going on in some part of Europe where, yeah, something happened at some point which changed priorities at the customer.
So it took Actually years I would say. Because one thing is settling on the requirements. Another thing is also it’s a big investment. So committing to that, that, that takes some time. Is it quicker to build than it is to specify then? Not at all. I don’t, when, once we got, there was a big pause.
So that’s, that shouldn’t be part of that. So once we got into the specification phase, it was a, it was a pretty intense months. But really good cooperation between the three of us.
Allen Hall: And RD is going to open the facility. in 2025. 2025. Yes. So how soon before it then becomes commissioned and ready to take that first main bearing, is it ready to go day one there?
Peter Winther: That’s the intention. Yes. The expectation. So right now, process wise we’ve left site, we’ve made the foundation and now we’ve stepped back a little bit. And now the building is being erected around it. It’s easier to make the big concrete block first and then build the building around it.
So they’re making the floor as we speak, they might finish that already. And then they’ll build the walls around it and then come start next year. It’s the intention. We’ll come back in and start installing auxiliaries and the test load unit and.
Joel Saxum: You know you’re making a big piece of kit when the building has to be built around it.
Allen Hall: So obviously R& D Test Systems is the leader in big test equipment and building these test benches. There’s, you do impressive work. How much is on your plate at the minute? You have this 25 megawatt facility going in. Are there other things already in the pipeline to, that you haven’t even announced yet?
That, that. You’re working on. How busy are you right
Peter Winther: now? We’re busy realizing the projects we have. And, unfortunately, I’m not allowed to tell too much about the pipeline, but we definitely have some interesting stuff going on. That’s for sure.
Allen Hall: That’s the beauty of R& D test systems. If you need somebody to build a piece of test equipment for big machines, you And do it right.
I would imagine there’s only one place to go and that’s R& D test systems. And you’re going to have to get ahold of Peter because Peter is their salesperson.
Peter Winther: Give me a call. I’m not the only one, but I can promise our sales organization, our sales team will take good care of you. If you have that particular need, we’ll love to help you solve it.
How do they reach you? How do they contact you? We have our webpage on rdas. dk where there’s a contact information where they can reach us.
Allen Hall: Yeah. And Peter’s available on LinkedIn. So if you get desperate and you need to have a 25 megawatt main bearing test facility built in your backyard or 30,
you just reach out to Peter, he’s ready to take your phone call. And I, every time R& D test systems comes on the podcast, I’m always impressed because You’re doing such amazing things and it’s such a benefit to the industry and congratulations on that. Come on. I know how hard that is to do and I know how successful these test benches have been.
That’s truly amazing. So Peter, thank you for being on the podcast. It’s been wonderful to have you.
Peter Winther: We’re just a small piece of the puzzle and we’re just helping, trying to help this green transition and yeah, having wind succeed because it’s awesome.
378 bölüm
Todos los episodios
×Player FM'e Hoş Geldiniz!
Player FM şu anda sizin için internetteki yüksek kalitedeki podcast'leri arıyor. En iyi podcast uygulaması ve Android, iPhone ve internet üzerinde çalışıyor. Aboneliklerinizi cihazlar arasında eş zamanlamak için üye olun.